Digital Twins in Manufacturing: Enhancing Efficiency
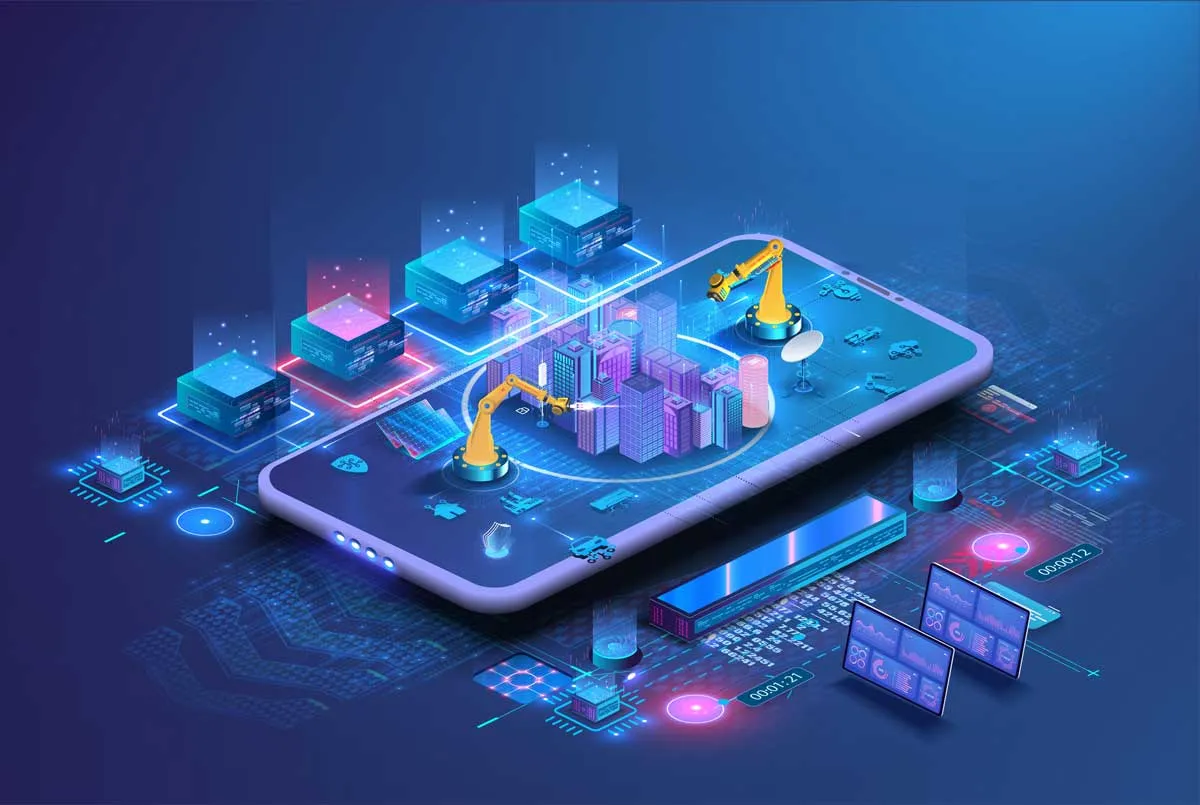
In the heart of modern manufacturing, a revolutionary technology is quietly transforming how industries operate: digital twins. Imagine having a virtual replica of your entire factory floor, every machine, and every product, right at your fingertips. This is the power of digital twins—virtual simulations that mirror physical assets and processes, providing unprecedented insights and opportunities for optimization.
Consider a manufacturing plant where digital twins are utilized to monitor and manage equipment performance. Sensors embedded in machinery collect real-time data on temperature, vibration, and operational metrics. This data is fed into digital twin models, creating accurate virtual representations of each machine. Manufacturers can then analyze these virtual twins to predict maintenance needs, schedule downtime proactively, and prevent costly breakdowns before they occur.
For process optimization, digital twins allow manufacturers to simulate and refine production workflows without disrupting actual operations. By tweaking parameters, testing scenarios, and identifying bottlenecks in a virtual environment, manufacturers optimize resource utilization, reduce waste, and streamline production efficiency. This iterative approach minimizes trial and error on the shop floor, leading to smoother operations and improved output.
Quality control is another area revolutionized by digital twins. In product development, virtual prototypes can be tested rigorously in a digital space before physical production begins. Engineers can simulate stress tests, analyze performance metrics, and detect potential defects—all within a virtual environment. This not only speeds up the product development cycle but also ensures that only the highest quality products reach the market.
Supply chain management benefits immensely from digital twins as well. By integrating real-time data from suppliers, logistics networks, and inventory systems, manufacturers gain visibility and control over their supply chains. Digital twins track inventory levels, monitor shipment statuses, and optimize delivery schedules, ensuring just-in-time production and minimizing stockouts or excess inventory.
The benefits of digital twins extend beyond operational efficiency to strategic decision-making. With real-time data analytics and predictive capabilities, manufacturers can make informed decisions quickly and confidently. Whether adjusting production schedules in response to market demand or optimizing resource allocation based on predictive maintenance insights, digital twins empower manufacturers to stay agile and competitive in dynamic market environments.
Of course, adopting digital twins comes with its challenges. Integrating data from diverse sources into cohesive digital twin models requires robust IT infrastructure and data management strategies. Ensuring data accuracy, reliability, and security is paramount to leveraging digital twins effectively. Moreover, developing expertise in digital twin technologies and simulation modeling is essential for maximizing their potential and driving continuous improvement in manufacturing operations.
Looking ahead, the future of digital twins in manufacturing looks promising. As advancements in artificial intelligence, machine learning, and IoT technologies accelerate, digital twins will become more sophisticated and autonomous. Imagine digital twins that not only monitor but also predict and prescribe actions based on real-time insights—optimizing operations, reducing costs, and driving innovation across global manufacturing sectors.
In conclusion, digital twins represent more than just a technological innovation; they are a transformative force in manufacturing. By bridging the gap between physical assets and virtual simulations, digital twins empower manufacturers to unlock new efficiencies, enhance decision-making capabilities, and drive sustainable growth. As industries continue to embrace digital transformation, digital twins will undoubtedly play a pivotal role in shaping the future of manufacturing, paving the way for smarter, more resilient, and agile operations in the digital age.