AI in Predictive Maintenance for Industrial Equipment
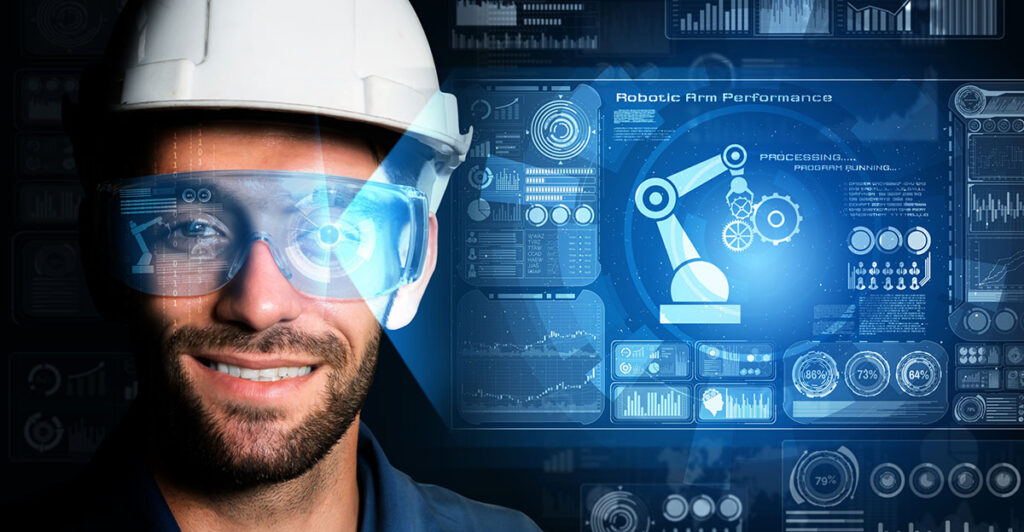
The industrial sector has always been at the forefront of adopting technologies that enhance efficiency, reduce costs, and improve overall productivity. One such transformative technology is predictive maintenance, which leverages artificial intelligence (AI) to anticipate equipment failures before they occur. By predicting when a machine is likely to fail, businesses can perform maintenance at the optimal time, thereby minimizing downtime and extending the lifespan of their equipment. This blog explores the role of AI in predictive maintenance, its benefits, and how it is reshaping industrial operations.
Predictive maintenance involves using data-driven approaches to predict the future state of equipment and scheduling maintenance activities accordingly. Traditional maintenance strategies, such as reactive maintenance (repairing equipment after it fails) and preventive maintenance (performing regular maintenance at scheduled intervals), have their limitations. Reactive maintenance can lead to unexpected downtime and costly repairs, while preventive maintenance may result in unnecessary maintenance activities and wasted resources. Predictive maintenance, on the other hand, aims to perform maintenance only when it is actually needed, based on the condition of the equipment.
AI plays a crucial role in predictive maintenance by analyzing large volumes of data collected from various sensors embedded in industrial equipment. These sensors monitor parameters such as temperature, vibration, pressure, and acoustic signals, providing real-time insights into the equipment’s operational status. AI algorithms, particularly machine learning models, process this data to identify patterns and anomalies that indicate potential issues. By continuously learning from the data, these models can accurately predict when a component is likely to fail, allowing maintenance teams to take proactive measures.
One of the primary benefits of AI-driven predictive maintenance is the reduction of unplanned downtime. Equipment failures can cause significant disruptions in production processes, leading to financial losses and delayed deliveries. By predicting failures before they occur, predictive maintenance enables timely interventions, ensuring that machines operate smoothly and efficiently. This not only enhances productivity but also reduces the financial impact associated with unexpected downtime.
Another significant advantage of predictive maintenance is the extension of equipment lifespan. Regular maintenance based on the actual condition of the equipment helps prevent excessive wear and tear, reducing the likelihood of catastrophic failures. As a result, businesses can maximize the return on investment (ROI) from their machinery and delay costly capital expenditures on new equipment. Additionally, predictive maintenance can improve safety by identifying potential hazards and preventing accidents caused by equipment malfunctions.
Cost savings are a major driving force behind the adoption of AI in predictive maintenance. Traditional maintenance approaches often involve unnecessary inspections and part replacements, leading to higher operational costs. Predictive maintenance optimizes the use of resources by focusing on equipment that genuinely requires attention. This targeted approach minimizes labor costs, reduces the consumption of spare parts, and lowers the overall maintenance budget. Moreover, predictive maintenance can enhance inventory management by ensuring that spare parts are available when needed, reducing the need for large stockpiles.
The implementation of AI-driven predictive maintenance involves several key steps. First, businesses need to equip their machinery with sensors capable of collecting relevant data. These sensors should be strategically placed to monitor critical components and capture comprehensive information about the equipment’s condition. Next, the collected data is transmitted to a central system where it is processed and analyzed using AI algorithms. Cloud computing and edge computing technologies can be employed to handle the data processing and storage requirements.
Machine learning models are then trained on historical data to learn the normal operating behavior of the equipment and identify deviations from this norm. These models can be supervised (trained on labeled data) or unsupervised (trained to detect anomalies without labeled data). Once the models are deployed, they continuously analyze incoming data and generate predictions about potential failures. These predictions are typically accompanied by confidence scores, indicating the likelihood of a failure occurring within a certain time frame.
For predictive maintenance to be effective, it is essential to have a robust data management strategy in place. This includes ensuring the quality and integrity of the data, as well as implementing data governance policies to manage access and security. Businesses should also invest in training their maintenance teams to understand and act on the insights provided by the AI system. Collaboration between data scientists, engineers, and maintenance personnel is crucial to successfully integrating predictive maintenance into existing workflows.
Despite its numerous benefits, the adoption of AI-driven predictive maintenance is not without challenges. One of the primary challenges is the initial cost of implementing the necessary infrastructure, including sensors, data processing systems, and AI software. Small and medium-sized enterprises (SMEs) may find it difficult to justify these upfront costs, although the long-term savings and productivity gains can outweigh the initial investment.
Another challenge is the complexity of developing accurate machine learning models. Creating models that can reliably predict equipment failures requires a deep understanding of both AI and the specific machinery being monitored. This often involves a collaborative effort between domain experts and data scientists. Additionally, the models must be continuously updated and refined as new data becomes available, which requires ongoing monitoring and maintenance.
Data privacy and security are also critical considerations. The data collected from industrial equipment can be sensitive and proprietary, and businesses must ensure that it is protected from unauthorized access and cyber threats. Implementing robust cybersecurity measures and complying with relevant regulations is essential to safeguard the data and maintain trust with stakeholders.
AI-driven predictive maintenance is revolutionizing the way businesses maintain and manage their industrial equipment. By leveraging AI to predict equipment failures, businesses can reduce downtime, extend equipment lifespan, save costs, and improve safety. Despite the challenges involved in implementation, the long-term benefits make predictive maintenance an attractive proposition for forward-thinking organizations. As AI technology continues to evolve, we can expect even more sophisticated and accurate predictive maintenance solutions, further enhancing the efficiency and reliability of industrial operations.
Stay ahead with ITBusinessNews – Your trusted source for Technology and Business news. Fast & Precise